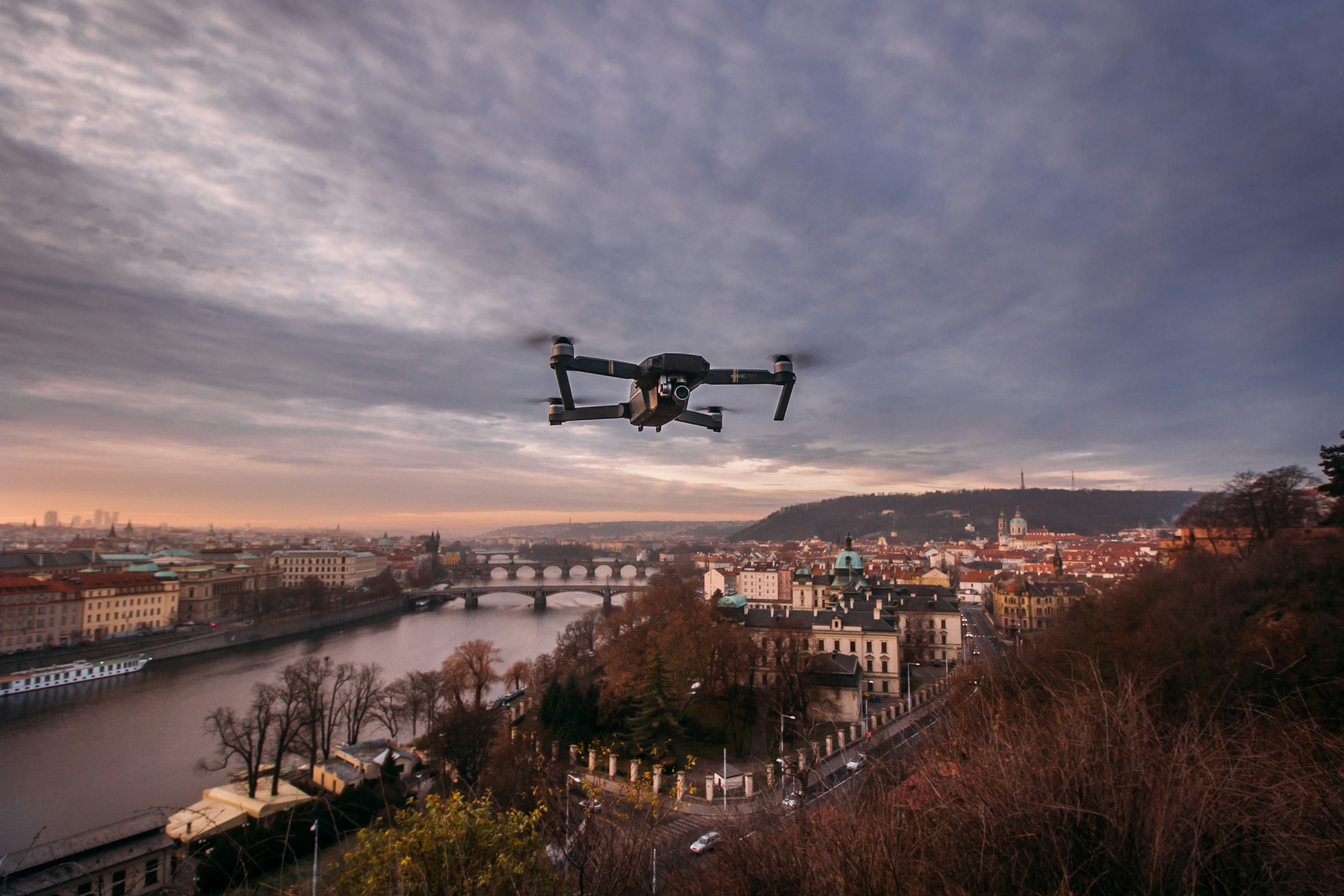
Portfolio Projects That Get You Hired for UAV Jobs (With Real GitHub Examples)
Unmanned Aerial Vehicles (UAVs), commonly known as drones, are reshaping industries—from aerial mapping and agriculture to disaster response and commercial delivery. As drone technology evolves rapidly, employers in the UAV sector are hungry for professionals with proven hands-on skills—be that in flight control, software integration, sensor fusion, or mechanical design. But how do you demonstrate these skills effectively? A robust UAV portfolio can help you stand out in a competitive job market. In this guide, we’ll cover: Why a UAV portfolio is crucial for demonstrating your capabilities. Choosing or designing UAV projects aligned with different drone-related roles. Real GitHub examples showcasing best practices in flight software, hardware integration, and autonomous control. Actionable project ideas to boost your portfolio right away. Best methods for presenting your work—ensuring recruiters see your impact immediately. Finally, we’ll point you to how you can connect your portfolio to real job openings, starting with a reminder to upload your CV on UAVJobs.co.uk so that employers seeking drone talent can easily find you.